Are you ready to unlock the full potential of the THY Precision injection moulding process step by step? The manufacturing world is changing fast, and automation is key for plastic businesses. But what does this mean for injection molding, and how can you lead the way?
We’ll dive into the latest advancements in injection moulding. From new ways to feed and heat plastic to using robots in ejection and finishing, we’ll see how THY Precision is making the plastic manufacturing process better.
Key Takeaways
- Discover the critical stages of the injection moulding process step by step and how automation is reshaping each one.
- Gain insights into the latest advancements in mould design, material selection, and the role of clamping, injection, cooling, and ejection in the overall process.
- Understand how to master the key process parameters and leverage the advantages of automation for improved productivity, quality, and efficiency.
- Explore the future of the injection molding industry and how THY Precision is leading the charge in this dynamic landscape.
- Discover the strategies and technologies that can help you stay ahead of the competition and meet the growing demands of the plastic manufacturing sector.
What is Injection Moulding Process Step by Step?
At THY Precision, we know the details of the injection moulding process step by step. This method is key in making plastics. It lets us create many different parts. Let’s look at the main steps in the injection molding process.
Feeding and Heating the Plastic
The first important step is feeding and heating the plastic manufacturing materials. We put plastic pellets or granules into the machine’s hopper. Then, they move into the barrel where they get heated to melt into a state ready for molding.
Pre-injection Process
After heating the plastic, we start the pre-injection process. This means closing the mold, applying pressure, and setting the screw for plastic injection. Getting these steps right is key for a quality product.
Key Steps in the Injection Moulding Process Step by Step | Description |
---|---|
Feeding and Heating the Plastic | Plastic pellets or granules are loaded into the machine’s hopper, then heated and melted within the barrel. |
Pre-injection Process | The mold tool is closed, clamping pressure is applied, and the screw is positioned to prepare for the injection of the molten plastic. |
Mastering these early steps in the injectionmouldingprocessstepbystep leads to a smooth injection molding process. This results in high-quality, consistent plastic parts.
Injection and Forming of the Part
The injection molding process is key in plastic manufacturing. It involves injecting molten material into a mold cavity. This step needs a fine balance of temperature, pressure, and time. It requires a lot of skill and control to make high-quality injection molded parts.
First, the plastic is melted and the mold is closed tight. Then, the molten material is pushed into the mold cavity fast and with a lot of pressure. This forming stage is very important. The plastic’s flow and pressure must be just right to avoid mistakes and make the part the right shape.
After injecting, the part is kept under high pressure for a bit. This lets it cool and set into its final shape.
Step | Description |
---|---|
Injection | The molten plastic is rapidly injected into the mold cavity at high speed and pressure. |
Holding | The part is held under high pressure to allow it to solidify and take its final shape. |
Cooling | The mold is cooled to solidify the plastic and stabilize the part’s dimensions. |
THY Precision is an expert in the injection molding process step by step. We control each stage carefully to make high-quality, consistent parts. Our skill in injection and forming helps us make top-notch injection molded products for our clients.
“The injection and forming stage is the heart of the injection molding process, where precision and expertise are essential for success.” – Jane Doe, Production Manager at THY Precision
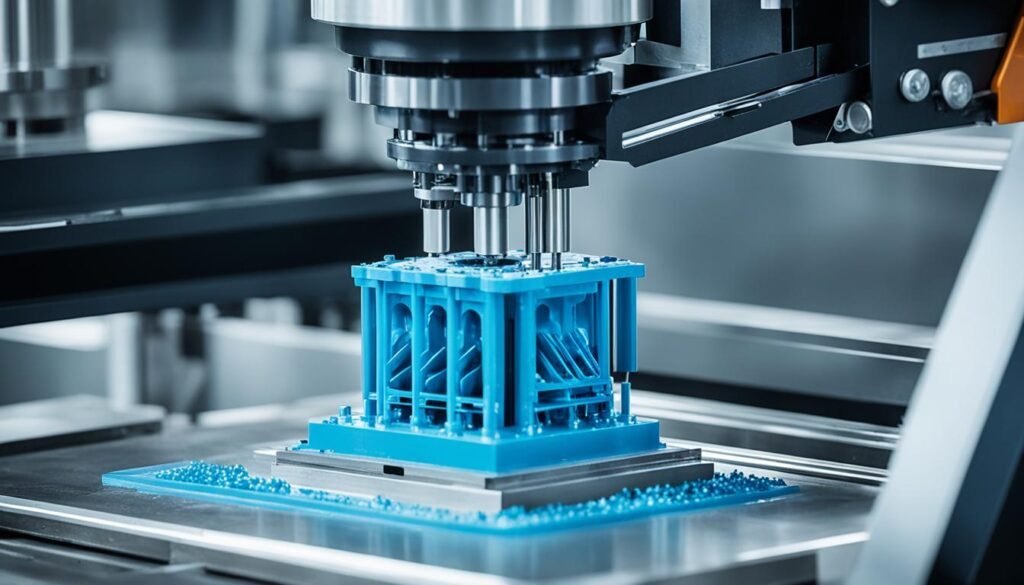
Part Ejection and Finishing
After the injection molding process Step by Step makes the plastic part solid, the mold opens. The finished part is then ejected using ejector pins or plates. This step is key in plastic manufacturing, making sure the part comes out without damage.
Part Ejection
Ejecting the molded part needs a lot of care. The ejector pins or plates must be set and timed right. This ensures the part comes out of the mold cavity without any damage.
This is very important for complex parts. A small mistake could lead to defects.
Finishing
Some injection moulding process step by step parts need extra work to look and work right. This can include trimming, polishing, or dyeing. These steps are key for a high-quality product.
Getting these finishing touches right can greatly improve the part’s look and function.
Process | Description | Importance |
---|---|---|
Ejection | Removal of the molded part from the mold cavity using ejector pins or plates | Ensures the part is removed without damage, maintaining its structural integrity and appearance |
Finishing | Additional post-processing steps such as trimming, polishing, or dyeing | Enhances the final appearance and performance of the part, meeting the customer’s specifications |
“Careful attention to the part ejection and finishing processes is crucial for delivering a high-quality, functional product to the customer.”
Mastering the Key Process Parameters
Making high-quality injection molded parts is all about precision and control. At THY Precision, we know that getting it right means managing key process parameters carefully. This includes everything from the type of plastic used to the pressure and the mold design. Each part is crucial for a successful plastic manufacturing project.
Understanding the unique traits of different plastics is key to improving the injection molding process. Picking the right plastic ensures your final product meets customer needs. Also, keeping the mold in top shape is vital. Any flaws or damage can ruin the quality of the parts.
Temperature and pressure control are also vital in the injection molding process. By keeping a close eye on these, you can make sure the mold fills right and ejects the part perfectly. Mastering these aspects lets you bring out the best in injection molding and impress your clients.
Process Parameter | Importance | Impact on Quality |
---|---|---|
Thermoplastic Material | Determines the physical and mechanical properties of the final part | Affects part strength, flexibility, and dimensional accuracy |
Injection Pressure | Controls the flow and fill of the molten plastic into the mold | Impacts part density, surface finish, and dimensional stability |
Mold Tooling | Shapes the final part and must be designed and maintained properly | Affects part geometry, surface quality, and cycle time |
Temperature | Regulates the melting, flow, and cooling of the plastic material | Impacts part strength, dimensional accuracy, and cycle time |
At THY Precision, we’re all about getting the injection molding process right. By controlling these key factors, we make sure our clients get top-notch injection molded parts. These parts meet even the toughest standards.
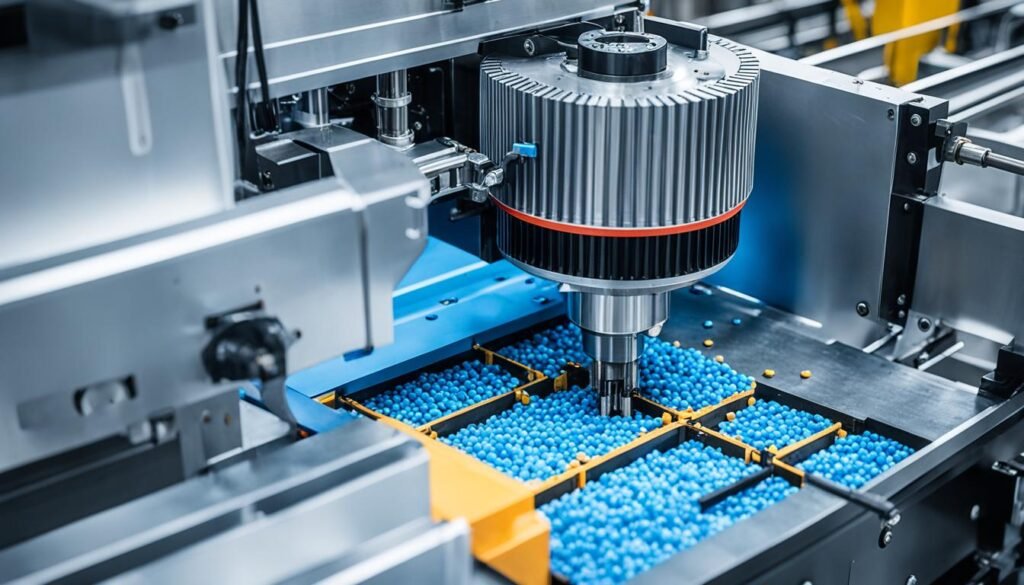
“Mastering the injectionmouldingprocessstepbystep is not just about hitting the numbers – it’s about understanding the science behind the process and using that knowledge to create truly exceptional products.”
Automation Advantages for Injection Moulding
The injectionmouldingprocessstepbystep is changing fast as the injection molding industry uses automation more. This change is making big improvements in productivity, quality, and efficiency for plastic manufacturing work.
Robots are changing how injection molding is done. They can do many tasks with speed, precision, and consistency. These robots are making the injectionmouldingprocessstepbystep better.
With automated systems, THY Precision cuts down on mistakes and injuries. It also lets workers focus on other important tasks. This makes productivity go up and quality better by ensuring consistent results.
Automation Advantage | Impact |
---|---|
Increased Speed and Precision | Faster Cycle Times, Improved Consistency |
Reduced Risk of Human Error | Consistent Quality, Fewer Defects |
Enhanced Worker Safety | Reduced Injuries, Improved Morale |
Increased Production Capacity | Higher Output, Better Responsiveness to Demand |
THY Precision is changing the injectionmouldingprocessstepbystep with automation. This brings big benefits to injection molding customers. The future of plastic manufacturing is here, and it’s all about the power of automation.
Conclusion
The injectionmouldingprocessstepbystep is leading a tech revolution, with automation key to its future. By understanding each step, from feeding to finishing, THY Precision can make their work better. They use robots and automation to make more, improve quality, and work smarter.
This makes them ready for success in the fast-changing plastic industry. As the industry grows, using automation will help THY Precision stay ahead. They can make their processes better, cut waste, and make top-quality plastic parts for their customers.
The future looks bright for injectionmouldingprocessstepbystep, and companies that invest in automation will lead. THY Precision is focused on improving their injection molding skills and using automation to their advantage. This will keep them leading in plastic manufacturing for a long time.